In WW Technic we care about the environmental impact. Therefore we are always working hard, to join the environmentally important projects. The generation of green energy is one of the most important topics in recent years. Sustainable economy is one of the ways to reduce carbon footprint, and we would like to present to You, Salo, and Vantaa projects, where we help to turn waste into energy.
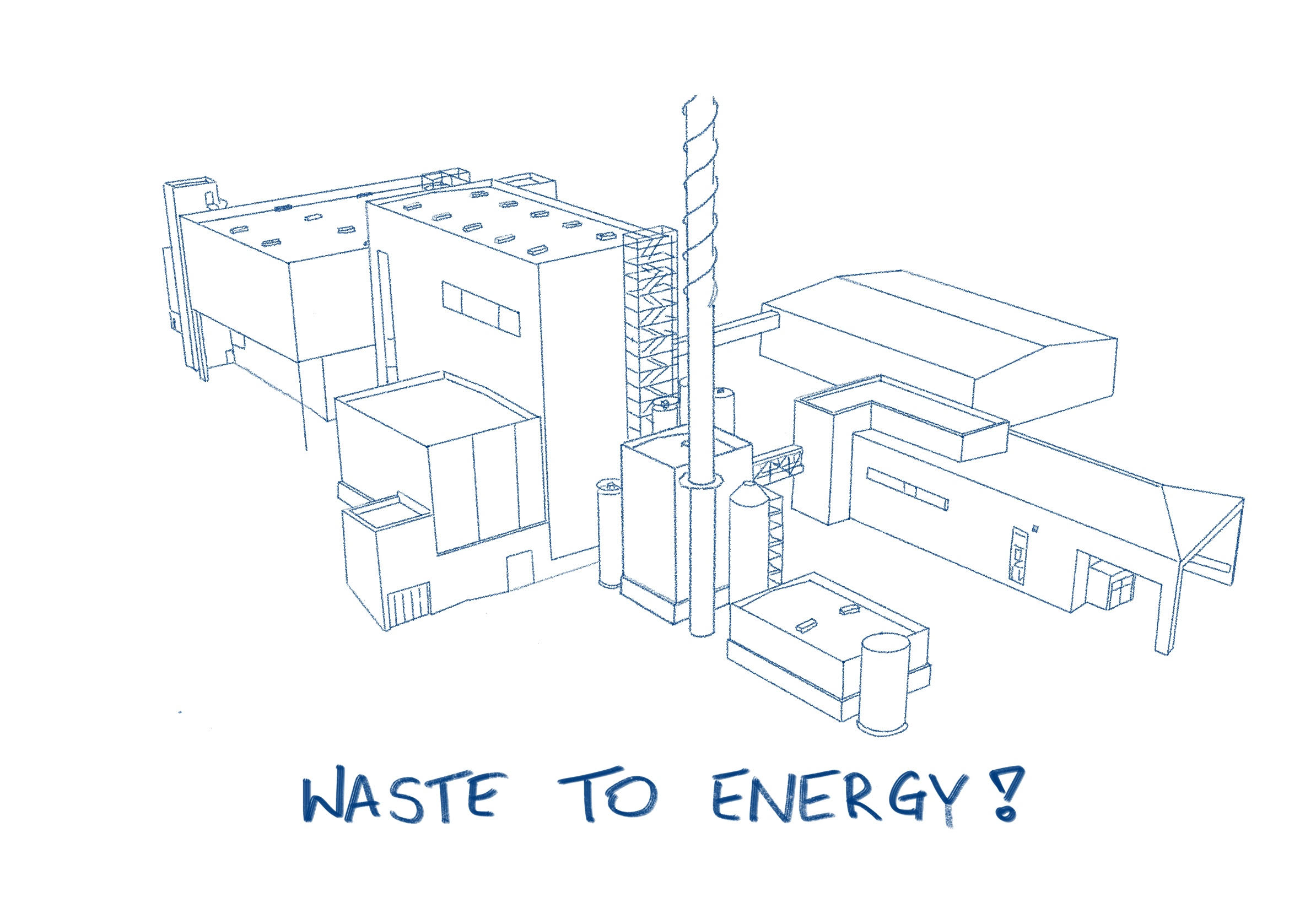
WW Technic first steps in turning waste into energy.
The first project on our roadmap was Salo in Finland. WW Technic was represented by Sławomir Dykstas, Radosław Wróblewski and Przemysław Kwiecień. This was for all of us our first project in this area of engineering. Therefore we need to combine our complex knowledge of hydraulics, burning processes, electrical, automation, and mechanical engineering. This was a challenge by its own, to provide a team
with such a wide expertise.
Second realization in these areas of engineering was realized in Vantaa, also Finland. The last team member – Przemyslaw Kwiecien left the project in May 2023. Both projects have been similar, but not exactly the same. As cities of Vanta and Salo are completely different in size, capacity, and power/heat generation. Technical challenges during both projects have been different.
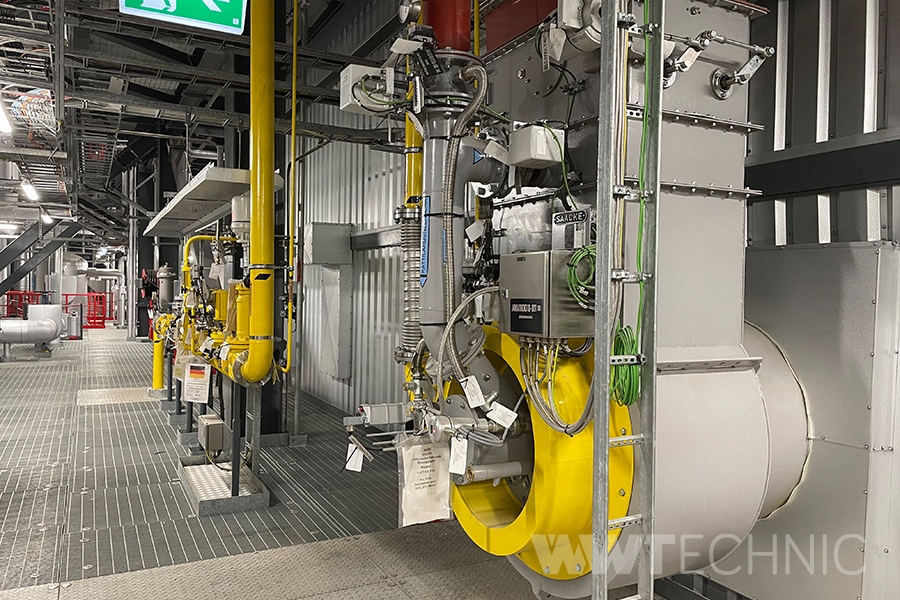
Technical details and challenges in the project
During Salo project WW Technic was involved at the end of installation phase. Sławomir Dykstas was responsible for installation inspections, its coordination and quality check . He also kept track on formal side as all handover documents were required to start the pre-commissioning phase. We need to prepare all sub-suppliers to pre-test their systems, to confirm that all components and subsystems are ready to perform. Only after successful setting up different components and all functionality test between subsystems we have been ready to start proper commissioning. All system acceptance tests were required, before we could? start a proper commissioning. From the very beginning we faced many challenges what required immediate solutions. From the very beginning we faced many challenges what required immediate solutions. As projects are finished we positively went through and solved all. Such size projects always surprise, create unpredictable situations and require deep cooperation.
After successful setting up to work different components, and subsystems we have been ready to start a proper commissioning.
Technical components on waste to energy project
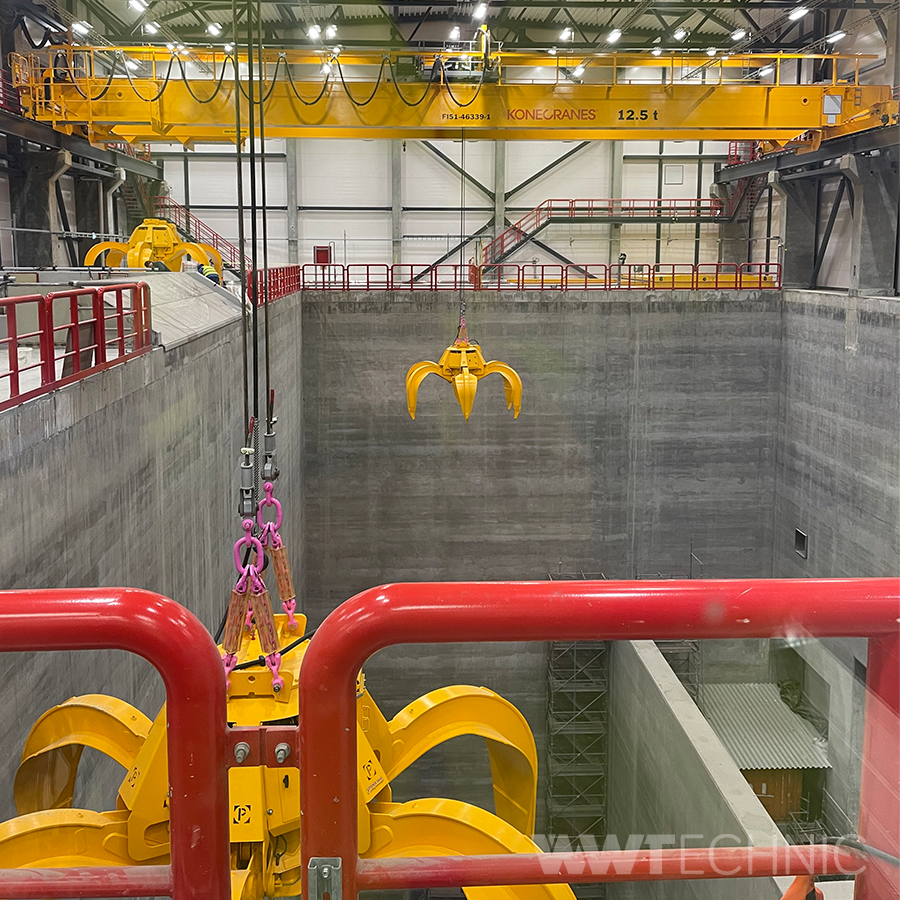
The next step was the commissioning of the complete system. We need to coordinate tests of a following components:
Hydraulic system – how to discharge garbage?
1) Waste Feeding: Hydraulic systems are used to control the feeding of waste materials into the incineration or gasification chambers, ensuring a steady and controlled supply of waste.
Role of Compressed air in waste to energy system
2) Compressed air system in waste-to-energy project is a versatile tool that supports combustion, emission control, material handling, and overall process control. It helps maintain operational efficiency, safety, and environmental compliance while ensuring the successful conversion of waste materials into usable energy
What is a role of a water system in waste to energy system?
3) Supply water system – plays the role of cooling, steam generation, emission control, material handling, and overall process support. It is a fundamental resource for maintaining the efficiency and safety of waste-to-energy facilities and is integral to the successful conversion of waste materials into usable energy while complying with environmental regulations.
Cooling system – important component
4) Cooling water system is essential for managing heat generated during combustion or gasification, recovering thermal energy, and maintaining the safe and efficient operation of the facility. It plays a pivotal role in ensuring environmental compliance, energy efficiency, and the overall success of converting waste into usable energy.
Fuel burner – heart of a waste to energy system
5) Fuel and burner system is at the heart of a waste-to-energy project, as it facilitates the controlled and efficient combustion or gasification of waste materials. It plays a pivotal role in ensuring energy recovery, emission control, temperature regulation, and safety while converting waste into usable energy.
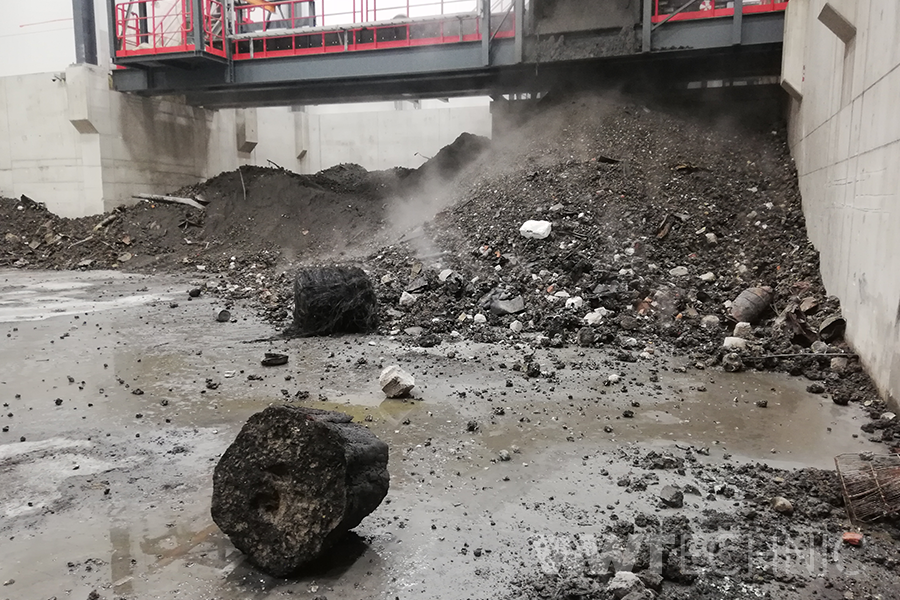
Burner creates exhaust
6) Exhaust system is essential for collecting, transporting, and treating the emissions and byproducts generated during waste conversion. It helps to reduce the environmental impact of the facility while meeting emission standards and ensuring safe and efficient waste-to-energy operations.
How to manage emmissions? Chemical processes behind
7) Chemical dosing system is critical for controlling emissions, capturing pollutants, and meeting environmental regulations. It enhances the efficiency and safety of waste-to-energy processes while ensuring compliance with emission standards and environmental requirements.
Technicall challenges during setting up to the system
All these test require a proper scheduling, because of very dangerous testing. Burner creates high temperature, boiler high pressures, cooling systems temperature control, etc. All these components create their own risks, which has to be taken into account. Therefore a big effort was scheduled a test in correct order. During commissioning, together with sub-supliers we discovered few required system updates.
There was few software and hardware upgrades, and all the way plant has started its trial period we worked on its optimization. Hardware changes included but were not limited to various medium lines modifications, required new sensors as well as replacements for better efficiency.
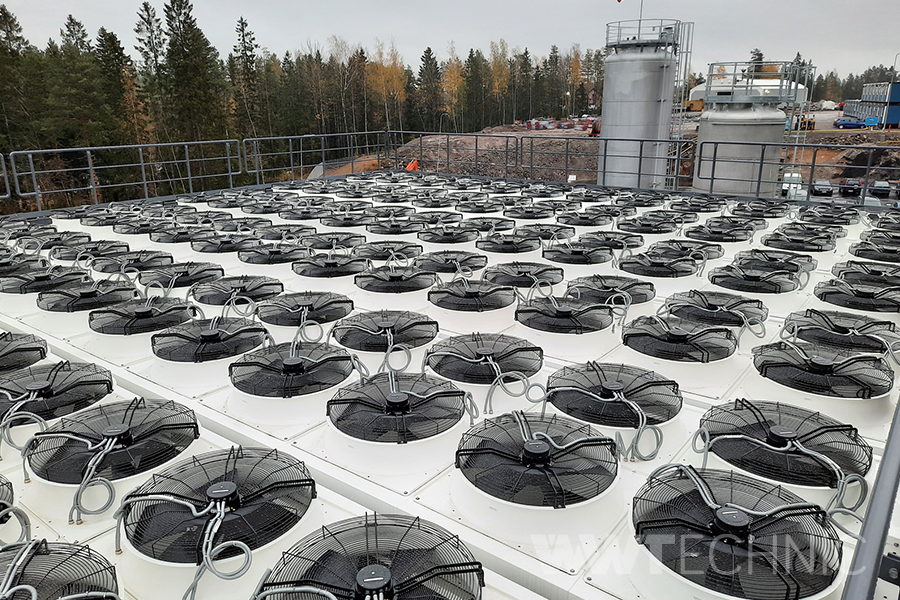
Orchestration of operation, and support during first operation period.
These two projects held particular significance for us, not only due to the incorporation of innovative technology but also because of our deep involvement in the entire process. Following the successful initial operation of the energy plant, our efforts shifted towards the essential task of training the operational crew. The Distributed Control System (DCS), serving as a Human-Machine Interface (HMI), enabled centralized remote control over all system components from our Control Centre. Our team took on the responsibility of verifying the correct functioning of all signals, with the final phase involving the comprehensive training of the operational crew. This crew training marked the concluding step in these
highly intricate projects.
Project summary
This has been a very complex project with a lot of different activities. We love to improve ourselves, therefore this was a great challenge for a WW Technic team. We have experience in commissioning of power plants, however, this was for a debut in waste to energy projects. So we are very happy, that we could successfully deliver the project in this domain. We also expect that we will be involved in more projects in this area. This is a good solution to reuse the garbage.
As WWT we are deeply involved in maritime market and energy sector. If You would like to work with us, feel free to apply over career page, here!